killie99
pfm Member
After many false starts and lots of almosts, I finally bought a TD124 Mk1. Serial number 42154 which I think suggests it was made in around 63/64 - if anyone knows a more accurate date please let me know.
As well as the 124, it came with a nice plinth, acrylic cover, SME309 and a Dynavector Karat 17D3.
On the outside it looks ok. The paint is actually in very good condition with hardly a blemish on it apart from 60 years of grime.
The top platter has been painted black, it doesn't have the iron platter but other than that, from above, it looked reasonably ok.
On power up it didn't sound great, some grinding and gnawing and was nowhere near running at the correct speed. Best not to run it again until it's been lubed ...
Took the platters off to see what was lurking underneath ...
It's a bit grubby but what do you expect from something that's been lurking around for 60 years?
Getting the TD124 out of it's plinth and turning it over was a little bit of a 'yikes' moment.
Hmm, a few bits of rust on the main bearing end cap and the motor casing and lots of hardened grease and oil.
I'm thinking the worst, the main bearing might be trashed and the motor might be trashed depending on where the rust has extended too.
Not a lot I can do about it now, just need to see what I can salvage.
I then took the whole table apart. Tried to photograph as much as I could to help me with the re-assembly and to give me an idea of how well I'll manage to clean it.
Fortunately I have an ultrasonic cleaning bath so most of the metal parts were popped in there in an attempt to clean the 60 years of oil/grease/grime. I disassembled everything prior to going in the bath and here's a before and after of the idler mechanism. Turned out quite well!
To be continued .....
As well as the 124, it came with a nice plinth, acrylic cover, SME309 and a Dynavector Karat 17D3.
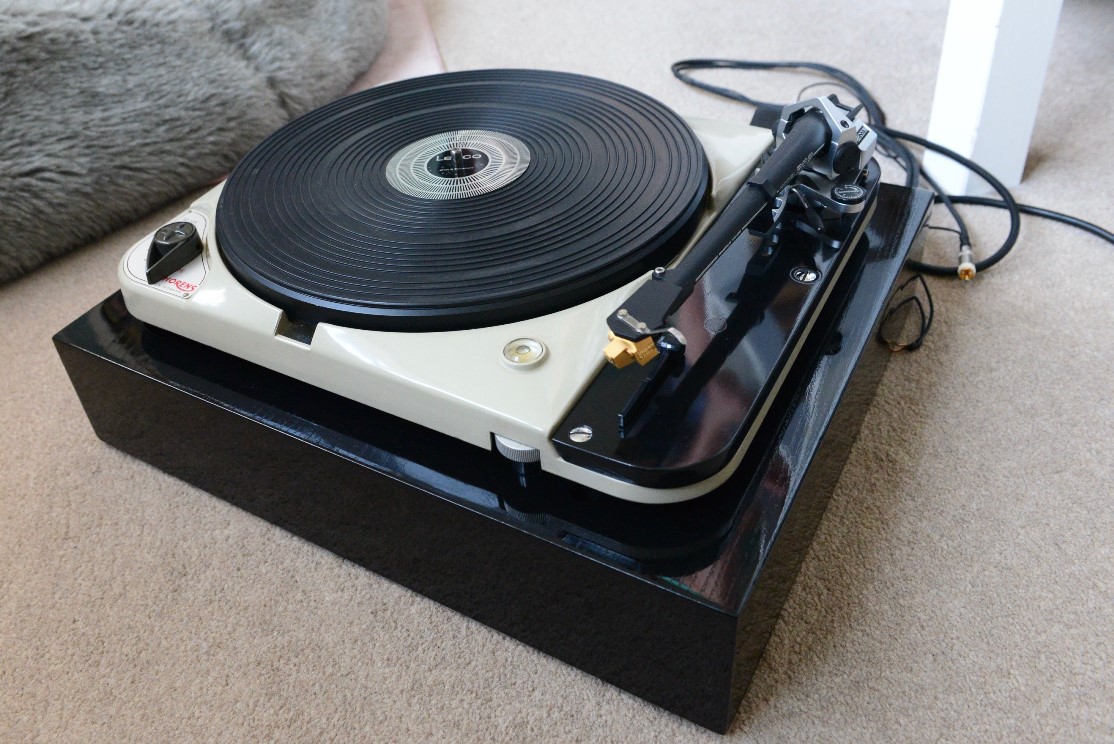
On the outside it looks ok. The paint is actually in very good condition with hardly a blemish on it apart from 60 years of grime.
The top platter has been painted black, it doesn't have the iron platter but other than that, from above, it looked reasonably ok.
On power up it didn't sound great, some grinding and gnawing and was nowhere near running at the correct speed. Best not to run it again until it's been lubed ...
Took the platters off to see what was lurking underneath ...
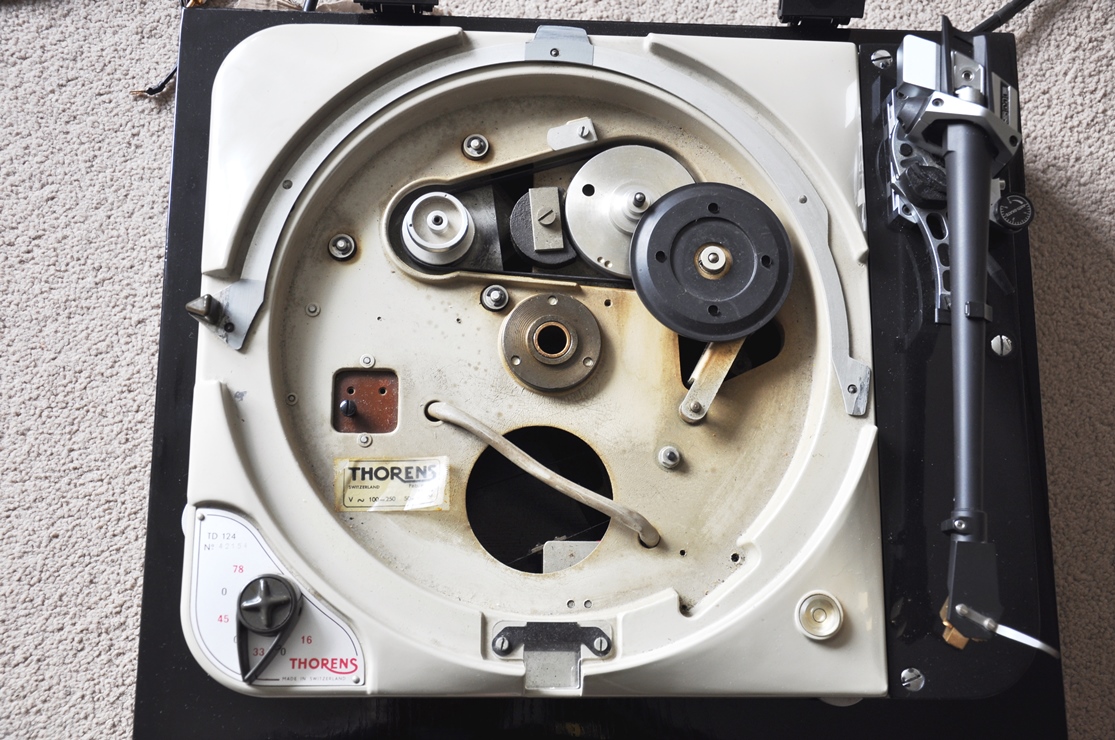
It's a bit grubby but what do you expect from something that's been lurking around for 60 years?
Getting the TD124 out of it's plinth and turning it over was a little bit of a 'yikes' moment.
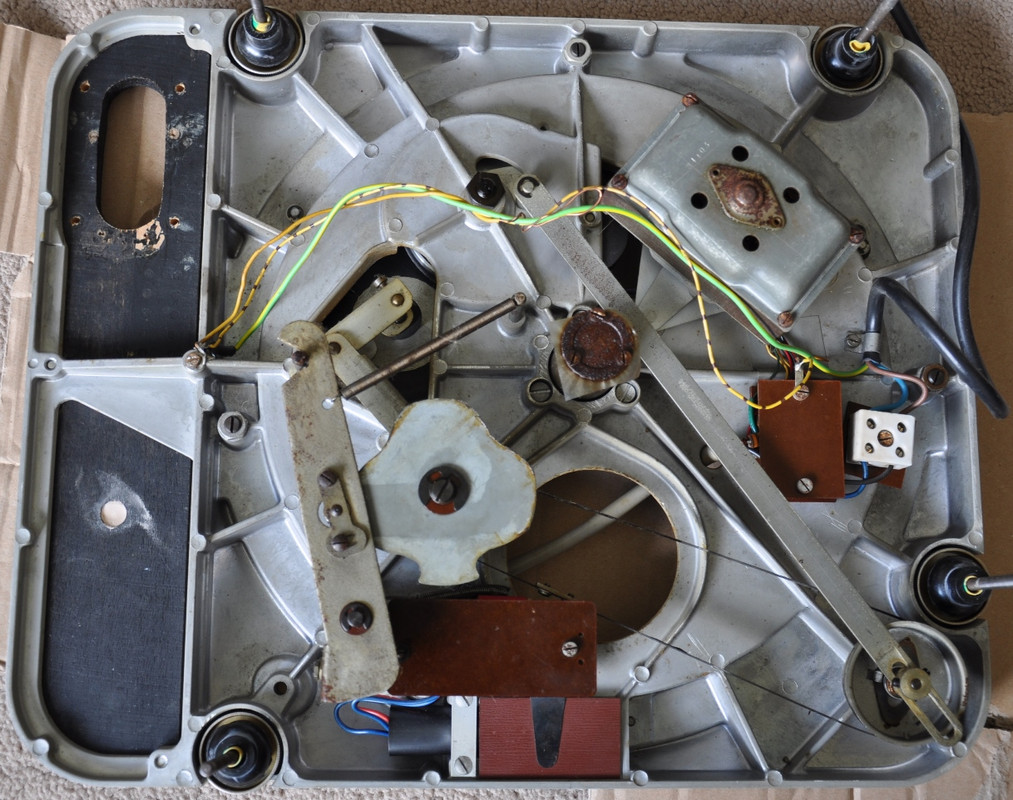
Hmm, a few bits of rust on the main bearing end cap and the motor casing and lots of hardened grease and oil.
I'm thinking the worst, the main bearing might be trashed and the motor might be trashed depending on where the rust has extended too.
Not a lot I can do about it now, just need to see what I can salvage.
I then took the whole table apart. Tried to photograph as much as I could to help me with the re-assembly and to give me an idea of how well I'll manage to clean it.
Fortunately I have an ultrasonic cleaning bath so most of the metal parts were popped in there in an attempt to clean the 60 years of oil/grease/grime. I disassembled everything prior to going in the bath and here's a before and after of the idler mechanism. Turned out quite well!
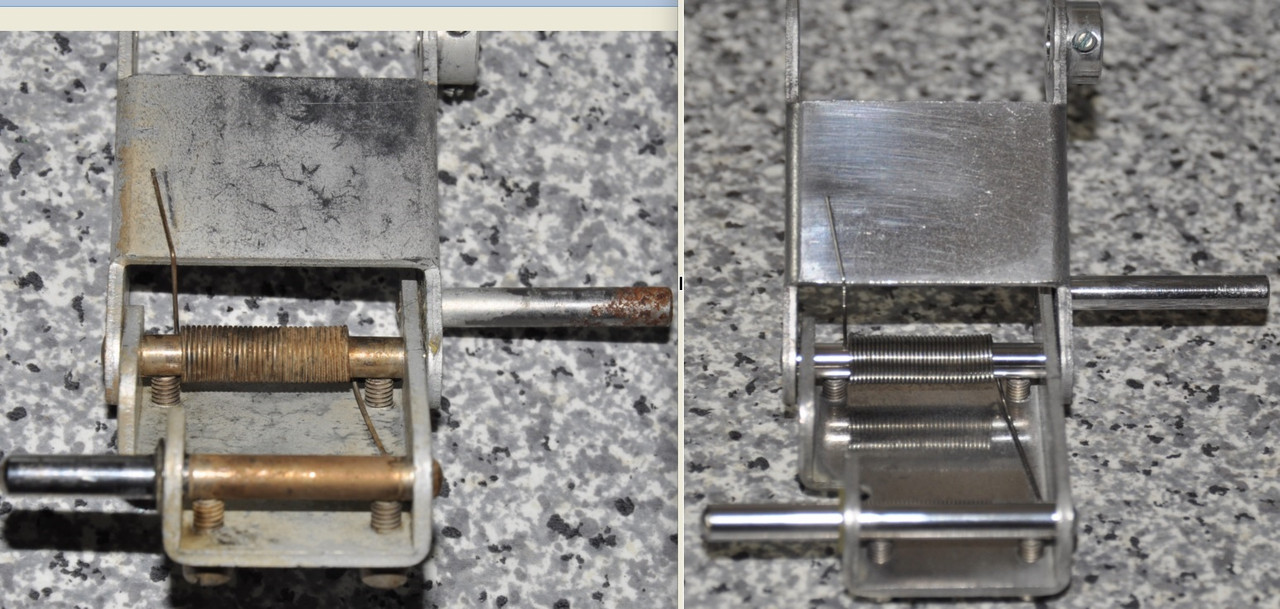
To be continued .....