vln
Shuns mooks. And MQA.
Just came across this:
Source: https://www.monoandstereo.com/?p=29309
As you can see, this is a wood screw they (Dynaudio) is using to fasten the bass drivers on their 10'000 EUR Focus 50 speakers - or am I seeing this wrong?
I would have expected that for a speaker at this price point (and frankly even below) you'd be using metal screws and metal threads...
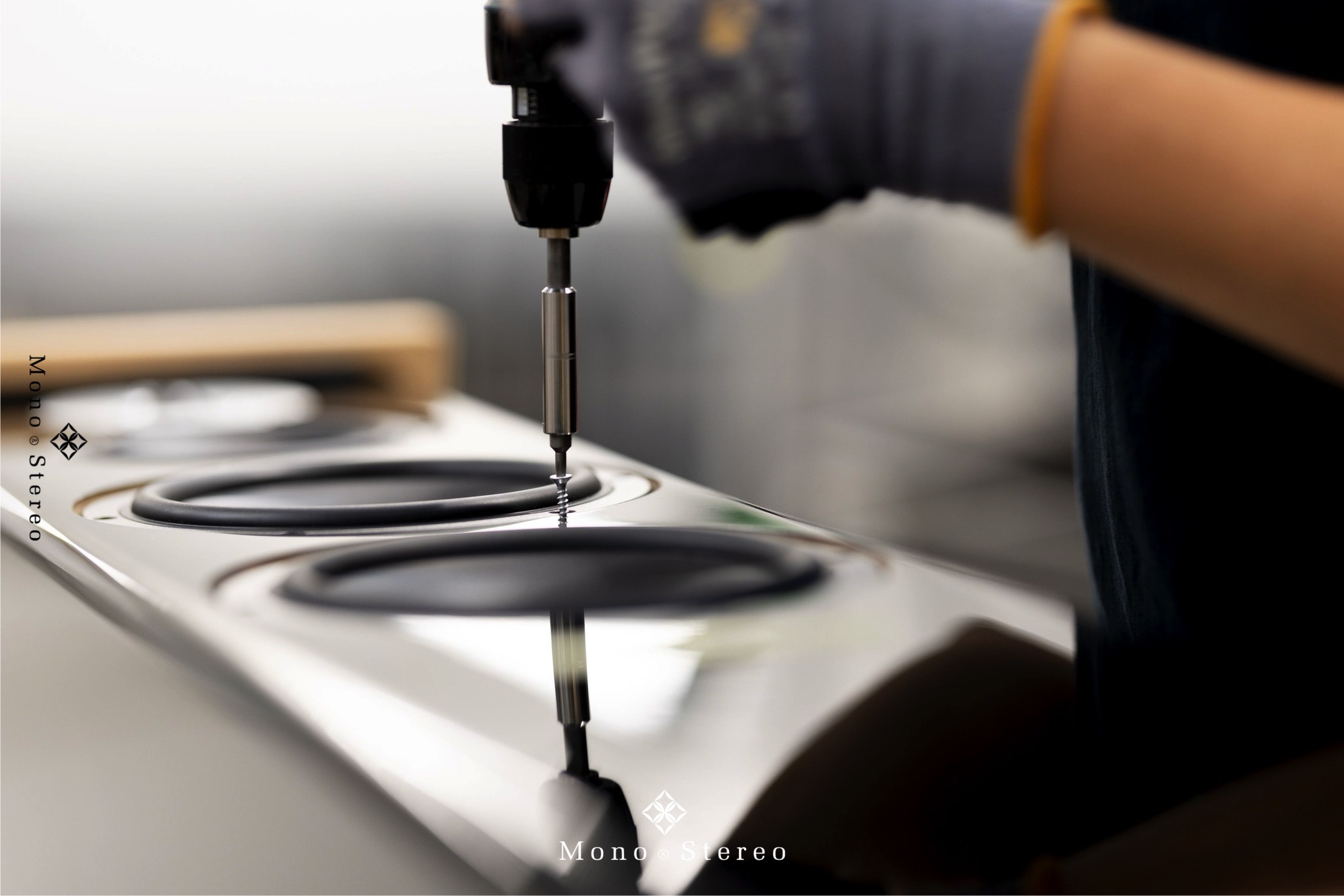
Source: https://www.monoandstereo.com/?p=29309
As you can see, this is a wood screw they (Dynaudio) is using to fasten the bass drivers on their 10'000 EUR Focus 50 speakers - or am I seeing this wrong?
I would have expected that for a speaker at this price point (and frankly even below) you'd be using metal screws and metal threads...